Introduction
In today's fast-paced manufacturing landscape, the impact of innovative techniques cannot be overstated. From advanced automation to sustainable practices, companies are revolutionizing their manufacturing processes to stay ahead of the competition. SSOURCING INC. is at the forefront of this transformation, helping businesses embrace change for sustainable growth and increased efficiency.
The Impact of Innovative Techniques in Manufacturing
The integration of innovative techniques in the manufacturing process has led to a significant increase in productivity and cost savings for companies across various industries. With the adoption of advanced technologies such as 3D printing and IoT, manufacturers are able to streamline their operations and deliver high-quality products at a faster pace.
Case Studies of Successful Manufacturing Process Transformation
Several industry leaders have successfully transformed their manufacturing processes through the implementation of innovative techniques. Companies like Tesla, Boeing, and Toyota have set a precedent for leveraging automation, 3D printing, and lean principles to achieve remarkable improvements in production efficiency and product quality.
Benefits of Implementing Innovative Techniques
The benefits of implementing innovative techniques in the manufacturing process are multifaceted. Not only do these advancements lead to higher productivity and reduced costs, but they also pave the way for greater sustainability and environmental responsibility. By embracing change and staying ahead of industry standards, companies can position themselves as leaders in their respective fields.
Implementing Advanced Automation
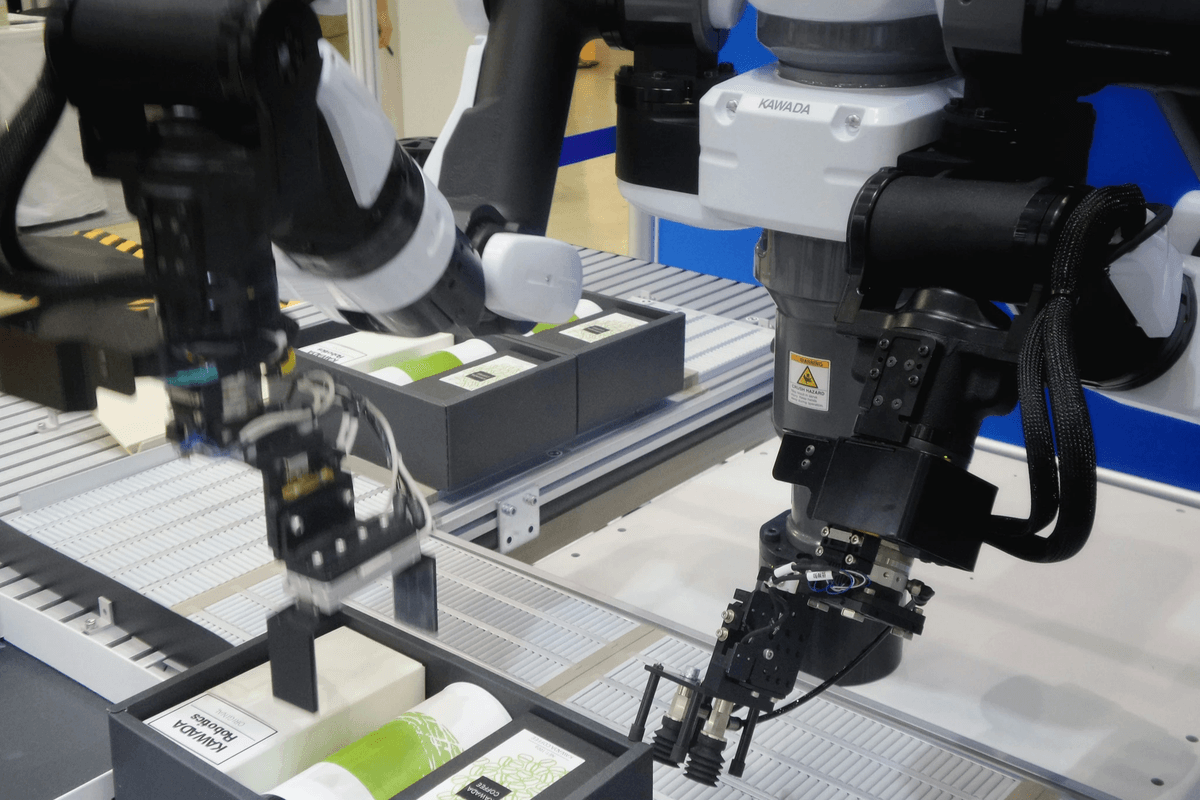
In today's competitive manufacturing landscape, the integration of advanced automation has become a game-changer for companies looking to enhance their manufacturing process. By incorporating robotics, manufacturers can streamline their operations, improve precision, and boost productivity. This innovative approach not only reduces the margin of error but also allows for faster production cycles, ultimately leading to increased output and cost savings for companies like SSOURCING INC.
Incorporating Robotics for Streamlined Manufacturing Process
The use of robotics in manufacturing has revolutionized the way products are made. With precise movements and consistent performance, robots can handle repetitive tasks with unparalleled accuracy, leading to a more efficient and streamlined manufacturing process. By leveraging this technology, SSOURCING INC. can optimize its operations, minimize errors, and maintain a competitive edge in the market.
Enhancing Efficiency with AI-based Manufacturing Tools
Artificial intelligence (AI) is another key player in advancing automation in manufacturing processes. AI-based tools can analyze vast amounts of data to identify patterns and make real-time adjustments to production lines, resulting in enhanced efficiency and reduced downtime. By implementing these tools, SSOURCING INC. can optimize its resource allocation, improve product quality, and stay ahead of market demands.
Case Study: How Tesla Revolutionized Production with Automation
Tesla's success story serves as a compelling case study on how advanced automation can revolutionize production processes. The company's utilization of robotic assembly lines and AI-powered predictive maintenance systems has enabled them to scale up production while maintaining high quality standards. As a result, Tesla has set new benchmarks for efficiency and innovation in the automotive industry.
By adopting advanced automation techniques such as robotics and AI-based tools, companies like SSOURCING INC. can achieve significant improvements in their manufacturing processes while staying ahead of the competition.
Utilizing 3D Printing Technology
3D printing has revolutionized the manufacturing process by offering a game-changing solution for rapid prototyping and customization. This innovative technology allows for the creation of intricate and complex designs with speed and precision, making it an invaluable tool for companies looking to stay ahead in the competitive market. SSOURCING INC. recognizes the potential of 3D printing in transforming traditional manufacturing processes and is committed to integrating this cutting-edge technology into our clients' production strategies.
A Game-Changer in Rapid Prototyping and Customization
The ability to quickly produce prototypes for testing and validation is crucial in today's fast-paced manufacturing environment. 3D printing enables manufacturers to rapidly iterate on designs, saving time and resources in the product development phase. SSOURCING INC. understands the importance of rapid prototyping in refining the manufacturing process, and we are dedicated to helping our clients leverage 3D printing technology to accelerate their innovation cycles.
Cost-Effective Production of Complex Components
Traditional manufacturing methods often struggle with producing complex components efficiently, leading to high costs and long lead times. With 3D printing, intricate parts can be produced without the need for specialized tooling or extensive manual labor, resulting in significant cost savings for manufacturers. At SSOURCING INC., we emphasize the cost-effective advantages of 3D printing technology in optimizing the overall manufacturing process for our clients.
Case Study: Boeing's Adoption of 3D Printing in Aerospace Manufacturing
Boeing, a leader in aerospace manufacturing, has embraced 3D printing as a game-changing innovation in their production processes. By leveraging this technology, Boeing has been able to manufacture lightweight yet durable components for their aircraft at a fraction of the time and cost compared to traditional methods. This case study serves as a testament to how forward-thinking companies can harness 3D printing to elevate their manufacturing capabilities and stay ahead of industry trends.
Lean Manufacturing Principles
Lean manufacturing is a strategic approach to optimizing the manufacturing process, focusing on minimizing waste and maximizing efficiency. By eliminating non-value-adding activities, companies can streamline their operations and enhance productivity. This method emphasizes the importance of continuous improvement and employee involvement in driving operational excellence.
Minimizing Waste and Maximizing Efficiency
Implementing lean manufacturing principles involves identifying and eliminating various forms of waste, such as overproduction, defects, waiting time, and unnecessary inventory. By streamlining processes and reducing these inefficiencies, manufacturers can significantly improve their overall operational efficiency. SSOURCING INC. understands the importance of lean manufacturing in achieving cost-effective production while maintaining high-quality standards.
The Role of Kaizen in Continuous Improvement
Kaizen, a Japanese term for continuous improvement, is a key component of lean manufacturing. It encourages employees at all levels to contribute ideas for incremental improvements in the manufacturing process. This culture of continuous improvement fosters innovation and drives sustainable growth within an organization. SSOURCING INC. recognizes the value of empowering employees to actively participate in process enhancements through Kaizen initiatives.
Case Study: Toyota's Lean Manufacturing Success
Toyota's renowned success in implementing lean manufacturing serves as a compelling case study for industry leaders seeking inspiration for operational excellence. By embracing principles such as Just-in-Time production and Total Quality Management, Toyota has set industry benchmarks for efficient production processes while maintaining exceptional product quality standards. SSOURCING INC.'s commitment to adopting best practices from successful case studies like Toyota's reinforces our dedication to driving innovation in the manufacturing sector.
Sustainable Manufacturing Practices
In today's competitive market, sustainable manufacturing practices have become a top priority for companies looking to reduce their environmental impact and enhance their brand reputation. By incorporating eco-friendly materials and integrating renewable energy sources into the manufacturing process, companies can significantly minimize their carbon footprint and contribute to a greener future. SSOURCING INC. is at the forefront of promoting sustainable manufacturing practices by advocating for the use of environmentally friendly materials and renewable energy sources in production.
Eco-Friendly Materials and Renewable Energy Integration
The use of eco-friendly materials such as recycled plastics, biodegradable packaging, and sustainable textiles not only reduces waste but also promotes a more circular economy. By integrating renewable energy sources like solar or wind power into the manufacturing process, companies can significantly reduce their reliance on non-renewable resources and decrease their overall environmental impact. SSOURCING INC. encourages its partners to adopt these sustainable practices to create a more environmentally friendly supply chain and manufacturing process.
Reducing Environmental Impact and Enhancing Brand Reputation
By embracing sustainable manufacturing practices, companies can effectively reduce their environmental impact while also enhancing their brand reputation as socially responsible entities. Consumers are increasingly drawn to brands that prioritize sustainability, leading to increased customer loyalty and positive brand perception. SSOURCING INC.'s commitment to sustainability not only benefits the environment but also elevates the reputation of its clients as leaders in responsible manufacturing.
Case Study: Patagonia's Sustainable Manufacturing Initiatives
Patagonia, a renowned outdoor clothing company, has set a remarkable example with its sustainable manufacturing initiatives. The company has implemented eco-friendly materials in its products while also investing in renewable energy integration across its supply chain. By doing so, Patagonia has not only reduced its environmental impact but has also strengthened its brand reputation as a champion of sustainability in the apparel industry.
Embracing IoT and Big Data Analytics
The integration of IoT and big data analytics has revolutionized the manufacturing process, allowing real-time monitoring for predictive maintenance. By leveraging IoT sensors and advanced analytics, manufacturers can proactively identify potential equipment failures, reducing downtime and maintenance costs. This technology enables SSOURCING INC. to optimize production schedules and minimize disruptions, ultimately enhancing operational efficiency.
Real-Time Monitoring for Predictive Maintenance
IoT sensors embedded in manufacturing equipment collect real-time data on machine performance, allowing for the early detection of potential issues before they escalate into costly breakdowns. With predictive maintenance, SSOURCING INC. can schedule repairs or replacements during planned downtime, preventing unexpected production interruptions and ensuring continuous workflow. This proactive approach not only saves time and money but also extends the lifespan of critical machinery, contributing to long-term sustainability.
Data-Driven Decision Making for Optimal Production
Big data analytics processes the vast amount of data generated by IoT devices to provide actionable insights for optimizing production processes at SSOURCING INC.. By analyzing historical performance data and current operational metrics, manufacturers can make informed decisions to improve efficiency, reduce waste, and enhance product quality. This data-driven approach empowers SSOURCING INC. to adapt quickly to changing market demands while maintaining high standards of manufacturing excellence.
Case Study: General Electric's Smart Factory Implementation
General Electric's implementation of smart factory technologies exemplifies the transformative impact of embracing IoT and big data analytics in manufacturing. By leveraging sensor-equipped machines and advanced analytics platforms, General Electric achieved significant improvements in operational efficiency, reduced maintenance costs, and enhanced product quality control. The seamless integration of IoT and big data analytics has positioned General Electric as a leader in innovative manufacturing practices.
Conclusion
In conclusion, the future of innovative manufacturing techniques is incredibly promising. With the rapid advancements in automation, 3D printing, lean principles, sustainable practices, and IoT integration, the industry is set for a revolution. Embracing change is crucial for sustainable growth and SSOURCING INC. is at the forefront of driving manufacturing innovation.
Unlocking Potential: Future of Innovative Manufacturing Techniques
The potential for innovative manufacturing techniques to revolutionize the industry is truly exciting. As we continue to witness the impact of automation, 3D printing, lean principles, and sustainable practices on manufacturing processes, it's clear that there are endless possibilities for improvement and growth. SSOURCING INC. recognizes this potential and is committed to leading the way in embracing these cutting-edge methods.
Evolving Industry Standards with Advanced Manufacturing Methods
The evolution of industry standards through advanced manufacturing methods is inevitable. The integration of robotics, AI-based tools, 3D printing technology, lean principles, and IoT analytics has already begun to reshape traditional manufacturing processes. As a forward-thinking company, SSOURCING INC. understands the importance of staying ahead of these changes and adapting to new standards.
Embracing Change for Sustainable Growth
Embracing change in manufacturing processes is not just about keeping up with trends; it's about ensuring sustainable growth for the future. By implementing innovative techniques such as advanced automation, 3D printing technology, lean principles, sustainable practices, and IoT integration, companies like SSOURCING INC. can position themselves as leaders in driving positive change within the industry.
The role of SSOURCING INC. in Driving Manufacturing Innovation
At SSOURCING INC., we take pride in our role as drivers of manufacturing innovation. By actively implementing advanced automation solutions, leveraging 3D printing technology for rapid prototyping and customization needs, embracing lean principles for efficient production processes, adopting sustainable practices to reduce environmental impact - we are setting new benchmarks in driving manufacturing innovation forward.